The Science Behind Cane Sugar Processing: Exactly How Sweet Taste is Fine-tuned
Wiki Article
Checking Out the Comprehensive Steps Included in Walking Stick Sugar Handling From Collecting to Refinement
The procedure of walking cane sugar production incorporates a series of intricate actions, beginning with the mindful harvesting of sugarcane and finishing in the improvement stages that make certain the final product fulfills sector standards. Each phase, from the extraction of juice to the purification and condensation procedures, plays a crucial role in figuring out the high quality and personality of the sugar. Understanding these stages not only highlights the intricacy of sugar production however also increases critical concerns concerning performance, sustainability, and innovation in the sector. What ramifications do these elements have for future techniques?Gathering Sugarcane
Gathering sugarcane is a vital action in the cane sugar handling chain, as it straight affects the high quality and yield of the end product. Correct timing and strategies are important throughout this stage to ensure optimal sugar material and decrease losses. Commonly, sugarcane is collected when it reaches maturation, normally 12 to 18 months after growing, defined by a high sucrose concentration.

Post-harvest, the sugarcane should be processed promptly to protect against sucrose degradation. Preferably, gathered walking cane ought to be moved to refining centers within 24-hour to maintain sugar top quality. For that reason, reliable logistical preparation is critical to keep the honesty of the harvested crop throughout the supply chain.
Removal Refine
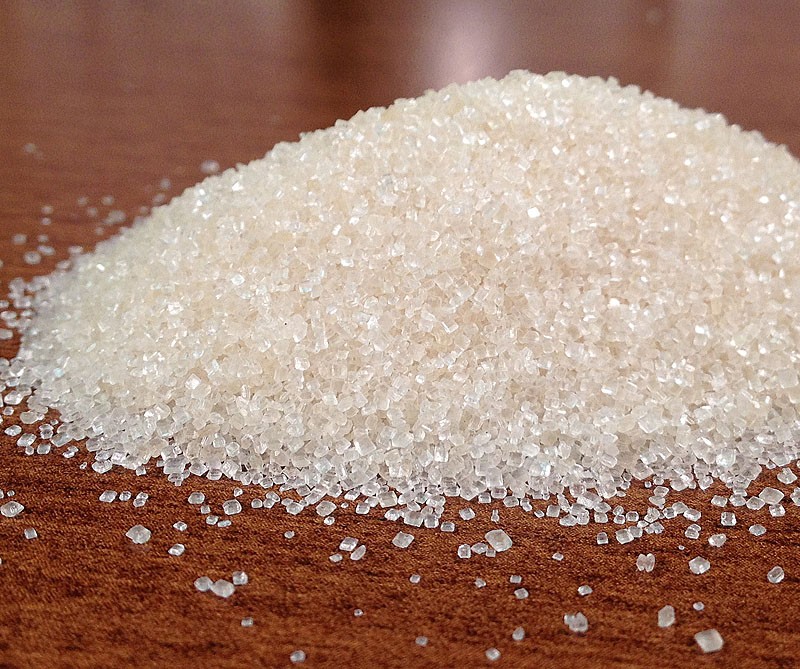
The crushed walking stick goes through a series of pressing operations to maximize juice recovery. Commonly, warm water is splashed onto the smashed walking stick, producing a countercurrent circulation that aids liquify the sugar while additionally aiding in the removal procedure. The juice collected from this procedure has not only sugar yet likewise various natural substances and impurities.
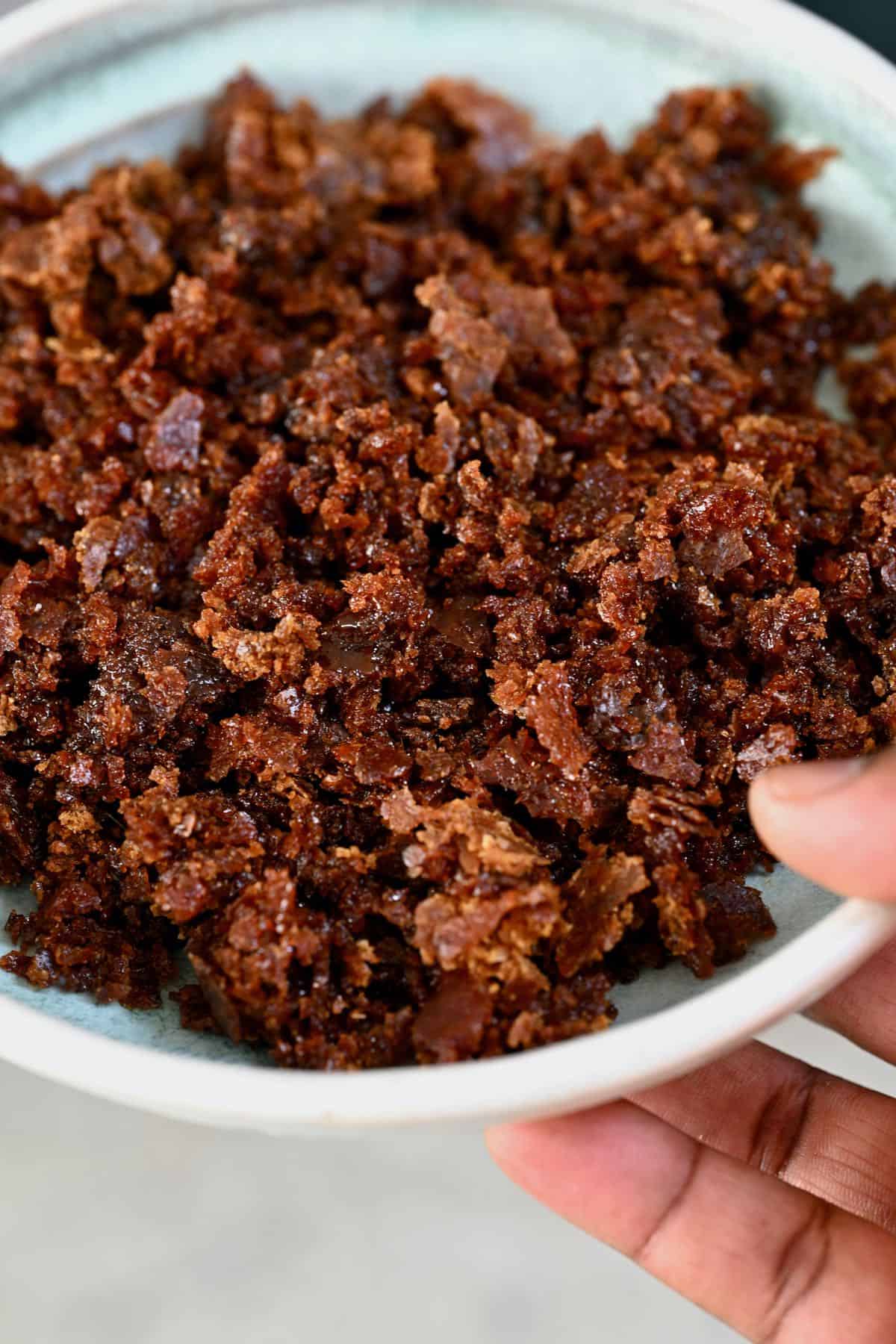
To improve removal efficiency, some centers may utilize diffusion approaches, where the sugarcane is taken in warm water, permitting the soluble sugars to diffuse into the liquid. The resulting juice, rich in sucrose, is after that guided to succeeding processing stages, laying the structure for filtration and refinement. The removal process is hence essential in identifying the quality and return of the final sugar product.
Filtration Strategies
The purification techniques used in walking stick sugar processing are vital for transforming the raw juice into a premium sugar item. These approaches largely aim to eliminate contaminations, such as dirt, plant products, and inorganic materials, which can negatively impact the end product's flavor and shade.Among one of the most common purification strategies is explanation. This procedure entails adding lime and heat to the raw juice, which promotes the coagulation of pollutants. The resulting precipitate is then removed via sedimentation or purification, producing a clearer juice. In addition, making use of phosphoric acid can improve the clarification procedure by more binding pollutants.
One more substantial strategy is carbonatation, where co2 is presented to the clarified juice. This reaction generates calcium carbonate, which records continuing to be contaminations and advertises their elimination.
Furthermore, triggered carbon therapy may be used to adsorb any kind of staying colorants and natural impurities, making sure an extra polished product. The combination of these techniques properly prepares the sugar juice for subsequent action in the refining procedure, setting the stage for the manufacturing of high-grade walking stick sugar.
Crystallization Approaches
After the filtration phase, the next essential step in walking stick sugar processing includes condensation methods, which play an essential function in transforming the made clear juice into strong sugar. This procedure Related Site usually utilizes two main methods: spontaneous crystallization and controlled crystallization.In spontaneous formation, supersaturated sugar solutions are enabled to cool down normally, leading to the formation of sugar crystals over time. This technique enables for the uniform growth of sugar crystals and greater pureness.
During crystallization, the cleared up juice is focused via evaporation, boosting its sugar web content up until it reaches supersaturation. As soon as this point is achieved, either technique can assist in the crystallization procedure. Cane Sugar Processing. The resultant sugar crystals are then divided from the continuing to be syrup via centrifugation
Eventually, the choice of crystallization technique influences the top quality, size, and purity of the final sugar product, making this step essential in the overall cane sugar processing procedure.
Improvement and Packaging
Just how can the purity and high quality of walking cane sugar be even more boosted after crystallization? The improvement process plays an important role in attaining high-grade cane sugar. Complying with condensation, sugar undertakes a thorough cleaning to eliminate impurities and recurring molasses. This is normally achieved making use of warm water or vapor, which helps liquify and extract undesirable aspects while preserving the sugar crystals.Following, the sugar is subjected to a process called centrifugation, where it is spun at broadband to divide the purified sugar crystals from the staying fluid. After centrifugation, the sugar is often more improved with an approach called carbonization or phosphatation, which makes use of turned on carbon or phosphoric acid to remove shade and off-flavors.
As soon as fine-tuned, the sugar is dried to attain the wanted dampness content, ensuring that it continues to be stable throughout storage and transport. The final step involves packaging the refined sugar in moisture-proof and impermeable containers to maintain its quality and prevent contamination. Cane Sugar Processing. Proper product packaging not just prolongs life span yet likewise promotes easy handling and distribution, making sure that customers receive sugar that satisfies the highest criteria of pureness and high quality
Conclusion
The extensive steps associated with walking cane sugar handling, from the thorough harvesting of sugarcane to the complex improvement and packaging phases, highlight the relevance of each stage in making certain premium sugar production. Ideal harvesting methods, efficient removal approaches, and strenuous filtration processes collectively add to the end product's purity and stability. The condensation and succeeding product packaging techniques additionally improve the stability and rack life of the sugar, highlighting the complexity and accuracy fundamental in this essential farming market.The process of cane sugar production encompasses a series of detailed steps, starting with the cautious harvesting of sugarcane and culminating in the refinement phases that make sure the last product satisfies market requirements. Preferably, collected walking cane must be delivered to processing facilities within 24 hours to maintain sugar high quality.In spontaneous crystallization, supersaturated sugar remedies are enabled to cool naturally, leading to the formation of sugar crystals over time - Cane Sugar Processing. The refinement process plays an important duty in attaining you could try here top quality walking cane sugar.The detailed click now actions entailed in cane sugar handling, from the thorough harvesting of sugarcane to the complex refinement and packaging phases, emphasize the relevance of each stage in making sure top notch sugar manufacturing
Report this wiki page